Kompresory to urządzenia mechaniczne, które mają na celu zwiększenie ciśnienia gazu poprzez zmniejszenie jego objętości.…
Jak połączyć dwa kompresory?
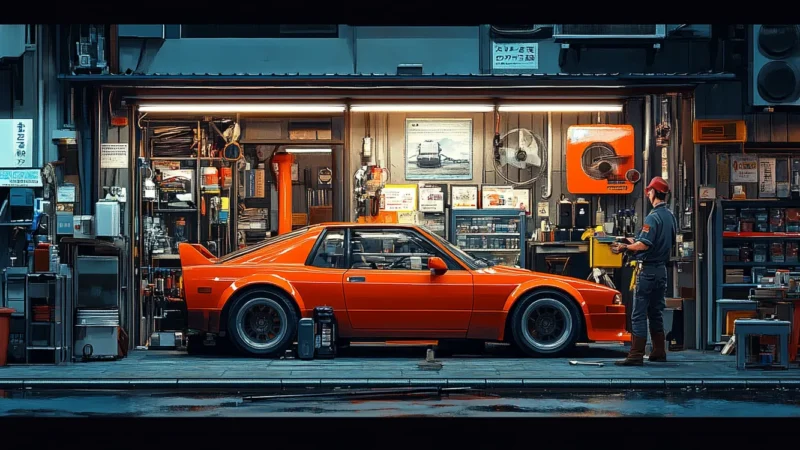
Łączenie dwóch kompresorów to proces, który wymaga staranności oraz zrozumienia zasad działania tych urządzeń. Przede wszystkim, przed przystąpieniem do jakichkolwiek działań, należy dokładnie zapoznać się z instrukcjami producenta obu kompresorów. Ważne jest, aby upewnić się, że oba urządzenia mają podobne parametry techniczne, takie jak ciśnienie robocze oraz wydajność. W przeciwnym razie może dojść do uszkodzenia jednego z kompresorów lub całego systemu. Kolejnym krokiem jest wybór odpowiedniego sposobu połączenia. Można zastosować różne metody, takie jak połączenie równoległe lub szeregowe. Połączenie równoległe pozwala na zwiększenie wydajności systemu, natomiast połączenie szeregowe umożliwia uzyskanie wyższego ciśnienia. Niezależnie od wybranej metody, kluczowe jest zapewnienie szczelności połączeń oraz użycie odpowiednich węży i złączek, które są dostosowane do pracy pod wysokim ciśnieniem.
Jakie narzędzia są potrzebne do połączenia kompresorów?
Aby skutecznie połączyć dwa kompresory, niezbędne jest przygotowanie odpowiednich narzędzi oraz materiałów. Przede wszystkim warto zaopatrzyć się w zestaw kluczy płaskich i nasadowych, które umożliwią dokręcenie wszystkich połączeń. Dodatkowo przyda się wkrętarka lub śrubokręt do montażu elementów konstrukcyjnych. W przypadku konieczności cięcia rur lub węży niezbędny będzie również piłka do metalu lub nożyce do rur. Oprócz narzędzi mechanicznych warto mieć pod ręką także materiały eksploatacyjne, takie jak uszczelki czy taśmy teflonowe, które zapewnią szczelność połączeń. Warto również pomyśleć o zakupie filtrów powietrza oraz separatorów wody, które poprawią jakość sprężonego powietrza i przedłużą żywotność kompresorów. Nie można zapomnieć o rękawicach ochronnych oraz okularach zabezpieczających, które zapewnią bezpieczeństwo podczas pracy.
Jakie błędy unikać przy łączeniu kompresorów?
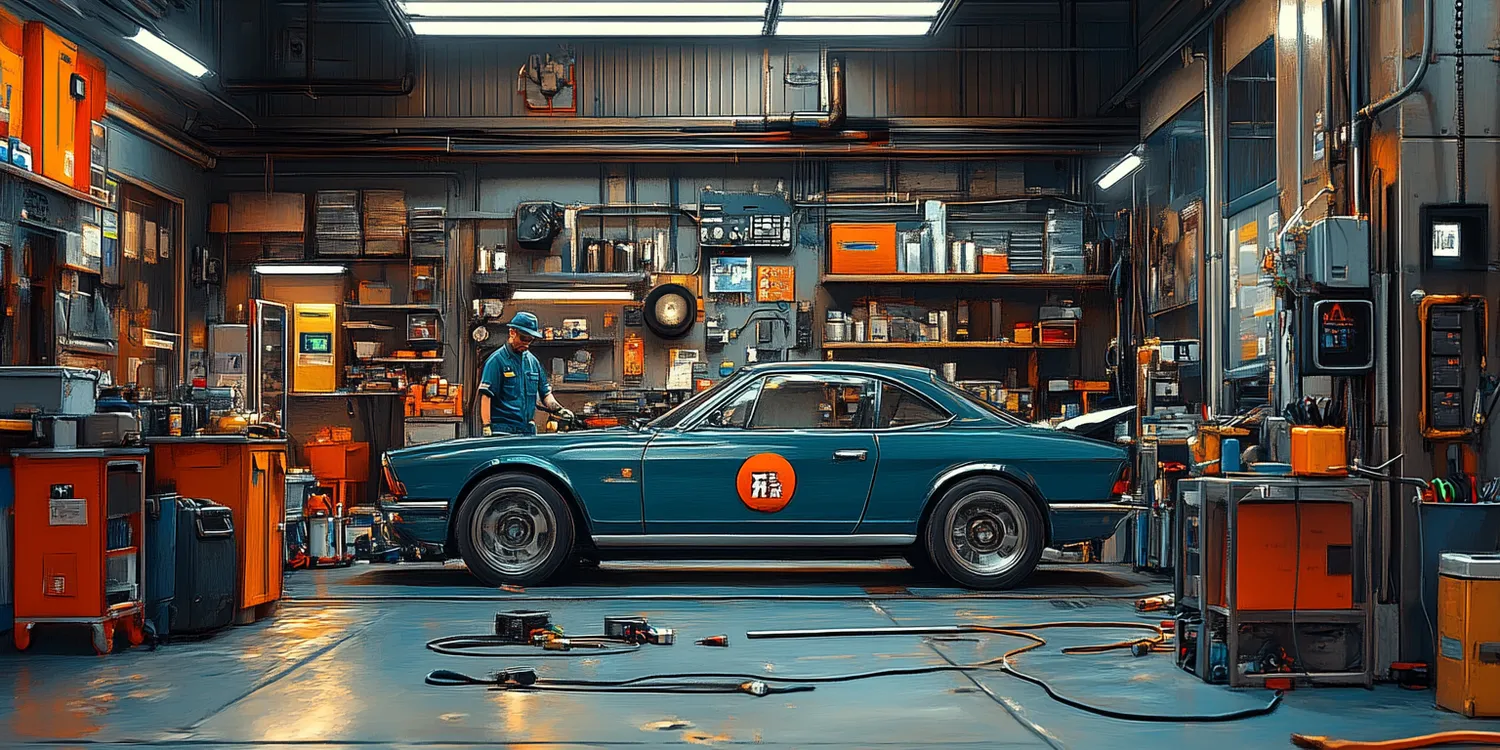
Podczas łączenia dwóch kompresorów istnieje wiele pułapek, które mogą prowadzić do problemów z działaniem całego systemu. Jednym z najczęstszych błędów jest niewłaściwe dobranie parametrów technicznych obu urządzeń. Użycie kompresora o znacznie wyższej wydajności niż drugi może prowadzić do jego przeciążenia i szybszego zużycia. Innym istotnym błędem jest niedostateczne zabezpieczenie połączeń przed wyciekami powietrza. Nieszczelności mogą prowadzić do spadku efektywności całego systemu oraz zwiększonego zużycia energii. Ważne jest również unikanie stosowania nieodpowiednich materiałów do połączeń, takich jak tanie węże czy niskiej jakości złączki, które mogą ulegać uszkodzeniom pod wpływem wysokiego ciśnienia. Należy także pamiętać o regularnym serwisowaniu obu kompresorów oraz monitorowaniu ich stanu technicznego. Ignorowanie tych kwestii może prowadzić do awarii oraz kosztownych napraw.
Jakie korzyści płyną z łączenia dwóch kompresorów?
Łączenie dwóch kompresorów niesie ze sobą wiele korzyści, które mogą znacząco wpłynąć na efektywność pracy w różnych branżach. Przede wszystkim pozwala na zwiększenie wydajności systemu sprężonego powietrza, co jest szczególnie istotne w zakładach przemysłowych czy warsztatach rzemieślniczych. Dzięki zastosowaniu dwóch kompresorów można osiągnąć większy przepływ powietrza oraz lepsze ciśnienie robocze, co przekłada się na lepszą jakość wykonywanych prac. Ponadto łączenie kompresorów daje możliwość elastycznego dostosowania systemu do zmieniających się potrzeb produkcji czy usług. W przypadku awarii jednego z urządzeń możliwe jest kontynuowanie pracy przy użyciu drugiego kompresora, co minimalizuje przestoje i straty finansowe związane z brakiem sprężonego powietrza. Dodatkowo inwestycja w dwa mniejsze kompresory może okazać się bardziej opłacalna niż zakup jednego dużego urządzenia o wysokiej wydajności.
Jakie są najczęstsze zastosowania połączonych kompresorów?
Połączenie dwóch kompresorów znajduje zastosowanie w wielu branżach, co czyni tę technikę niezwykle wszechstronną. W przemyśle budowlanym, gdzie zapotrzebowanie na sprężone powietrze jest znaczne, połączone kompresory mogą zasilać różnorodne narzędzia pneumatyczne, takie jak młoty udarowe czy wiertarki. Dzięki zwiększonej wydajności możliwe jest jednoczesne używanie kilku urządzeń, co przyspiesza prace budowlane i zwiększa ich efektywność. W warsztatach samochodowych połączone kompresory również odgrywają kluczową rolę, umożliwiając zasilanie narzędzi takich jak klucze pneumatyczne czy pistolety lakiernicze. W tym przypadku istotne jest nie tylko ciśnienie, ale także stabilność dostarczanego powietrza, co można osiągnąć dzięki odpowiedniemu połączeniu kompresorów. W przemyśle spożywczym oraz farmaceutycznym, gdzie jakość sprężonego powietrza ma kluczowe znaczenie, połączenie kompresorów pozwala na uzyskanie czystego i suchego powietrza, co jest wymagane w procesach produkcyjnych.
Jakie są koszty związane z łączeniem kompresorów?
Koszty związane z łączeniem dwóch kompresorów mogą się znacznie różnić w zależności od wielu czynników. Przede wszystkim należy uwzględnić cenę samych urządzeń. Jeśli planujemy połączyć dwa istniejące kompresory, to koszty będą ograniczone do zakupu niezbędnych akcesoriów i materiałów eksploatacyjnych. W przypadku zakupu nowych kompresorów warto zwrócić uwagę na ich parametry techniczne oraz producenta, co może wpłynąć na ostateczny koszt inwestycji. Dodatkowo konieczne będzie zainwestowanie w odpowiednie złącza, węże oraz manometry, które również generują dodatkowe wydatki. Koszty instalacji mogą być różne w zależności od skomplikowania systemu oraz lokalnych stawek za usługi hydrauliczne czy pneumatyczne. Warto również pamiętać o kosztach eksploatacyjnych związanych z energią elektryczną potrzebną do pracy obu kompresorów oraz regularnym serwisowaniem urządzeń.
Jakie są zalety korzystania z automatyki przy łączeniu kompresorów?
Wprowadzenie automatyki do systemu łączącego dwa kompresory może znacząco poprawić efektywność ich pracy oraz wygodę użytkowania. Automatyka pozwala na monitorowanie parametrów pracy obu urządzeń w czasie rzeczywistym, co umożliwia szybką reakcję na ewentualne problemy. Dzięki zastosowaniu czujników ciśnienia i przepływu można automatycznie dostosowywać pracę kompresorów do aktualnych potrzeb, co przekłada się na oszczędność energii oraz minimalizację strat powietrza. Systemy automatyki mogą również kontrolować cykle pracy kompresorów, co pozwala na równomierne obciążenie obu urządzeń i wydłuża ich żywotność. Dodatkowo automatyka umożliwia integrację z innymi systemami zarządzania produkcją, co zwiększa efektywność całego zakładu. Umożliwia to także zdalne monitorowanie stanu systemu oraz jego diagnostykę, co jest szczególnie istotne w dużych zakładach przemysłowych.
Jakie są najważniejsze zasady bezpieczeństwa przy łączeniu kompresorów?
Bezpieczeństwo podczas łączenia dwóch kompresorów jest kluczowym aspektem, który należy brać pod uwagę na każdym etapie procesu. Przede wszystkim przed rozpoczęciem pracy należy zapoznać się z instrukcjami obsługi obu urządzeń oraz przestrzegać wszystkich zaleceń producenta dotyczących montażu i eksploatacji. Ważne jest również stosowanie odpowiednich środków ochrony osobistej, takich jak rękawice robocze oraz okulary ochronne, które zabezpieczą przed ewentualnymi urazami mechanicznymi czy chemicznymi. Podczas montażu należy upewnić się, że wszystkie połączenia są szczelne i wykonane zgodnie z normami bezpieczeństwa. Niezbędne jest także regularne sprawdzanie stanu technicznego zarówno samych kompresorów, jak i elementów instalacji pneumatycznej. Warto również przeprowadzać okresowe przeglądy systemu przez wykwalifikowany personel techniczny, aby uniknąć potencjalnych awarii oraz zagrożeń dla zdrowia i życia pracowników.
Jakie są różnice między połączeniem równoległym a szeregowym kompresorów?
Połączenie równoległe i szeregowe kompresorów to dwie podstawowe metody łączenia tych urządzeń, które różnią się zarówno zasadą działania, jak i efektami końcowymi. Połączenie równoległe polega na tym, że oba kompresory pracują jednocześnie i dzielą obciążenie równomiernie między sobą. Taki układ pozwala na zwiększenie wydajności systemu sprężonego powietrza bez podnoszenia ciśnienia roboczego. Jest to idealne rozwiązanie w sytuacjach, gdy potrzebna jest duża ilość powietrza o stabilnym ciśnieniu do zasilania narzędzi pneumatycznych lub innych urządzeń wymagających dużego przepływu powietrza. Z kolei połączenie szeregowe polega na tym, że jeden kompresor zasila drugi, co prowadzi do podniesienia ciśnienia roboczego w systemie. Taki układ sprawdza się w sytuacjach wymagających wysokiego ciśnienia sprężonego powietrza do specyficznych zastosowań przemysłowych czy technologicznych.
Jakie są najlepsze praktyki przy konserwacji połączonych kompresorów?
Aby zapewnić długotrwałą i efektywną pracę połączonych kompresorów, konieczne jest przestrzeganie najlepszych praktyk konserwacyjnych. Regularna konserwacja obejmuje kontrolę stanu technicznego obu urządzeń oraz ich elementów składowych, takich jak filtry powietrza czy oleju. Należy pamiętać o wymianie filtrów zgodnie z zaleceniami producenta oraz monitorować poziom oleju w silnikach kompresorów. Kolejnym istotnym krokiem jest sprawdzanie szczelności wszystkich połączeń oraz uszczelek, aby uniknąć nieszczelności prowadzących do strat sprężonego powietrza. Ważne jest również regularne czyszczenie układów chłodzenia oraz wentylacji, które wpływają na efektywność pracy urządzeń. Warto także prowadzić dokumentację serwisową dla każdego z kompresorów oraz rejestrować wszelkie przeprowadzone naprawy czy wymiany części eksploatacyjnych.