Destylator laboratoryjny to urządzenie służące do separacji cieczy na podstawie różnicy w temperaturze wrzenia. W…
Destylator przemysłowy
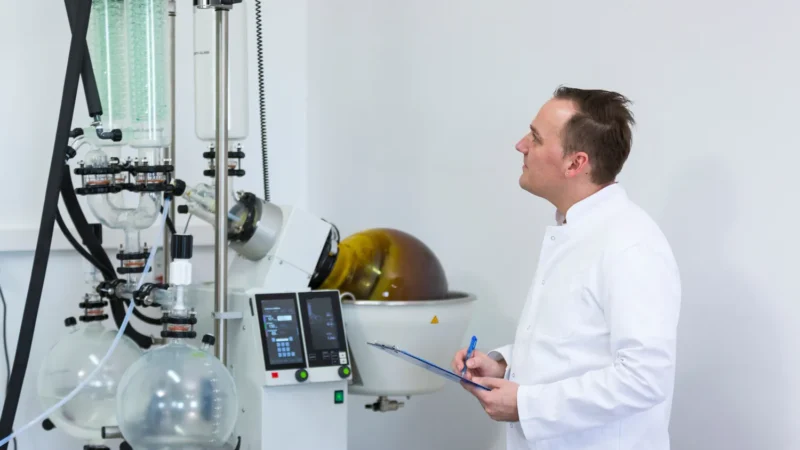
Destylator przemysłowy to urządzenie, które służy do oddzielania składników mieszanin cieczy na podstawie różnicy w temperaturze wrzenia. Proces ten jest kluczowy w wielu branżach, takich jak chemiczna, petrochemiczna czy spożywcza. W destylacji wykorzystuje się zjawisko parowania, gdzie ciecz o niższej temperaturze wrzenia przechodzi w stan gazowy, a następnie skrapla się w chłodnicy. W przemyśle najczęściej stosuje się destylację frakcyjną, która pozwala na oddzielenie wielu składników jednocześnie. Destylatory przemysłowe są zazwyczaj większe i bardziej skomplikowane niż ich laboratoryjne odpowiedniki, co pozwala na przetwarzanie dużych ilości substancji. W zależności od zastosowania, destylatory mogą być wyposażone w różne systemy kontrolne oraz automatyzację, co zwiększa efektywność procesu.
Jakie są rodzaje destylatorów przemysłowych i ich zastosowania
W przemyśle istnieje wiele rodzajów destylatorów, które różnią się konstrukcją oraz zastosowaniem. Najpopularniejsze z nich to destylatory prostokątne, kolumnowe oraz membranowe. Destylatory prostokątne są najczęściej wykorzystywane w procesach, gdzie wymagana jest wysoka czystość produktu końcowego. Charakteryzują się one prostą budową i łatwością w obsłudze. Z kolei destylatory kolumnowe są bardziej zaawansowane technologicznie i pozwalają na efektywne oddzielanie wielu składników jednocześnie dzięki zastosowaniu kolumny z wypełnieniem lub talerzami. Tego rodzaju urządzenia znajdują zastosowanie w produkcji alkoholi oraz olejów eterycznych. Destylatory membranowe natomiast są nowoczesnym rozwiązaniem, które wykorzystuje membrany do separacji składników na poziomie molekularnym. Są one szczególnie przydatne w przemyśle farmaceutycznym oraz chemicznym, gdzie wymagane są wysokie standardy czystości i efektywności procesów.
Jakie są korzyści z używania destylatorów przemysłowych
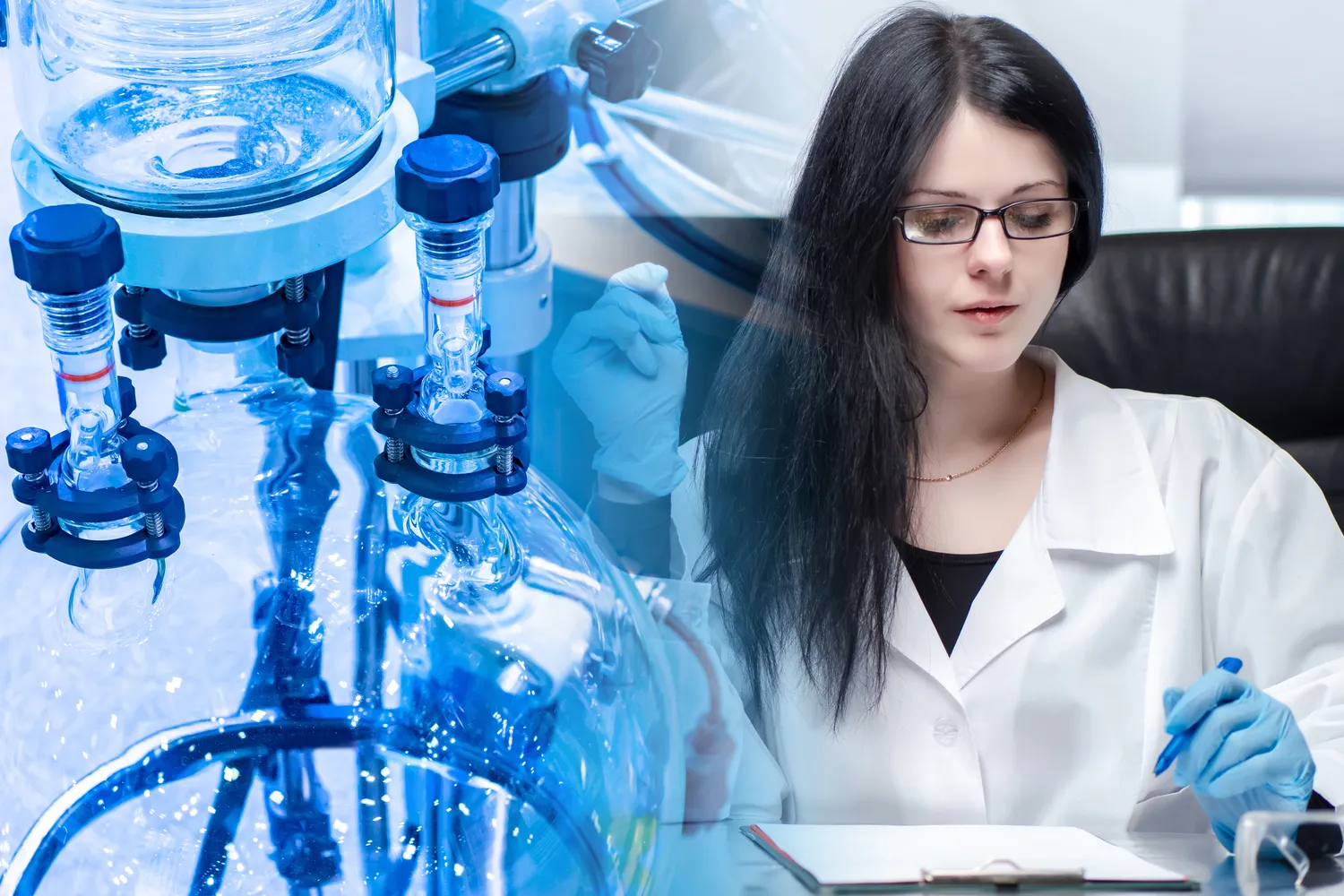
Użycie destylatorów przemysłowych przynosi wiele korzyści zarówno dla producentów, jak i dla konsumentów. Przede wszystkim umożliwiają one uzyskanie wysokiej jakości produktów poprzez skuteczne oddzielanie niepożądanych składników oraz zanieczyszczeń. Dzięki temu procesy produkcyjne stają się bardziej wydajne, a koszty związane z obróbką surowców znacznie maleją. Dodatkowo nowoczesne destylatory są często wyposażone w systemy automatyzacji i monitorowania, co pozwala na lepszą kontrolę nad procesem oraz minimalizację ryzyka błędów ludzkich. W kontekście ochrony środowiska warto zauważyć, że wiele nowoczesnych urządzeń charakteryzuje się zwiększoną efektywnością energetyczną oraz mniejszym zużyciem surowców. To sprawia, że procesy destylacyjne stają się bardziej ekologiczne i zrównoważone.
Jakie są wyzwania związane z eksploatacją destylatorów przemysłowych
Mimo licznych korzyści związanych z używaniem destylatorów przemysłowych istnieją także pewne wyzwania, które należy brać pod uwagę podczas ich eksploatacji. Jednym z głównych problemów jest konieczność regularnej konserwacji i serwisowania urządzeń, aby zapewnić ich prawidłowe działanie oraz uniknąć awarii. Niewłaściwe użytkowanie lub brak odpowiedniej dbałości o sprzęt mogą prowadzić do obniżenia jakości produktów oraz zwiększenia kosztów operacyjnych. Kolejnym wyzwaniem jest zarządzanie odpadami powstającymi podczas procesu destylacji. Wiele substancji chemicznych może być szkodliwych dla środowiska, dlatego ważne jest wdrażanie odpowiednich procedur recyklingu i utylizacji. Również zmiany regulacyjne dotyczące ochrony środowiska mogą wpływać na sposób działania zakładów przemysłowych korzystających z destylatorów.
Jakie są najnowsze technologie w dziedzinie destylacji przemysłowej
W ostatnich latach w dziedzinie destylacji przemysłowej nastąpił znaczny postęp technologiczny, który przyczynił się do zwiększenia efektywności i jakości procesów produkcyjnych. Jednym z najważniejszych osiągnięć jest rozwój destylacji membranowej, która pozwala na separację składników na poziomie molekularnym. Ta innowacyjna metoda charakteryzuje się wysoką selektywnością oraz niskim zużyciem energii, co czyni ją atrakcyjną alternatywą dla tradycyjnych metod destylacji. Kolejnym interesującym rozwiązaniem są systemy automatyzacji, które umożliwiają zdalne monitorowanie i kontrolowanie procesów destylacyjnych. Dzięki zastosowaniu zaawansowanych algorytmów sztucznej inteligencji oraz analizy danych, producenci mogą optymalizować parametry pracy urządzeń w czasie rzeczywistym, co prowadzi do zwiększenia wydajności i redukcji kosztów operacyjnych. Warto również wspomnieć o zastosowaniu nanotechnologii w budowie elementów destylatorów, co pozwala na poprawę ich wydajności oraz trwałości. Nowe materiały i technologie przyczyniają się do zmniejszenia strat ciepła oraz poprawy efektywności energetycznej całego procesu.
Jakie są kluczowe czynniki wpływające na wydajność destylatorów przemysłowych
Wydajność destylatorów przemysłowych jest determinowana przez szereg czynników, które należy uwzględnić podczas projektowania oraz eksploatacji tych urządzeń. Przede wszystkim istotne jest odpowiednie dobranie parametrów procesu, takich jak temperatura i ciśnienie. Zmiany tych wartości mogą znacząco wpłynąć na efektywność separacji składników oraz jakość uzyskiwanego produktu. Kolejnym ważnym aspektem jest rodzaj stosowanej kolumny destylacyjnej oraz jej konstrukcja. Kolumny z talerzami czy wypełnieniem mają różne właściwości hydrodynamiczne, co wpływa na efektywność wymiany masy między fazami cieczy i pary. Oprócz tego kluczowe znaczenie ma także jakość surowców wykorzystywanych w procesie, ponieważ obecność zanieczyszczeń może obniżyć wydajność destylacji oraz wpłynąć na jakość końcowego produktu. Nie można zapominać o regularnej konserwacji i serwisowaniu urządzeń, które pozwalają na utrzymanie ich w dobrym stanie technicznym oraz zapewniają stabilność procesów.
Jakie są zastosowania destylatorów przemysłowych w różnych branżach
Destylatory przemysłowe znajdują szerokie zastosowanie w różnych branżach, co świadczy o ich wszechstronności i znaczeniu w procesach produkcyjnych. W przemyśle chemicznym służą do separacji składników chemicznych, takich jak rozpuszczalniki czy kwasy, co pozwala na uzyskanie czystych substancji do dalszej obróbki. W branży petrochemicznej destylacja jest kluczowym procesem w produkcji paliw oraz olejów bazowych. Destylatory kolumnowe są szczególnie popularne w rafineriach, gdzie umożliwiają oddzielanie frakcji ropy naftowej według różnicy temperatur wrzenia. W przemyśle spożywczym destylatory wykorzystywane są do produkcji alkoholi oraz ekstraktów roślinnych, takich jak olejki eteryczne czy aromaty. Proces destylacji pozwala na uzyskanie wysokiej jakości produktów o intensywnym smaku i zapachu. Również w przemyśle farmaceutycznym destylatory odgrywają istotną rolę, umożliwiając oczyszczanie substancji czynnych oraz eliminację zanieczyszczeń chemicznych. Ponadto coraz częściej stosuje się je w sektorze biotechnologicznym do odzyskiwania bioetanolu czy innych biopaliw z biomasy.
Jakie są koszty związane z inwestycją w destylatory przemysłowe
Inwestycja w destylatory przemysłowe wiąże się z różnorodnymi kosztami, które należy uwzględnić przed podjęciem decyzji o zakupie lub budowie nowego zakładu produkcyjnego. Koszt samego urządzenia może być znaczny i zależy od jego typu, wielkości oraz zastosowanych technologii. Na przykład nowoczesne destylatory kolumnowe wyposażone w zaawansowane systemy automatyzacji mogą być znacznie droższe niż prostsze modele prostokątne. Dodatkowo należy brać pod uwagę koszty związane z instalacją i uruchomieniem urządzenia, które mogą obejmować prace budowlane oraz dostosowanie infrastruktury zakładu do nowych wymagań technologicznych. Koszty eksploatacyjne również odgrywają kluczową rolę – obejmują one zużycie energii, surowców oraz konserwację urządzeń. Regularne serwisowanie jest niezbędne dla utrzymania wydajności i jakości produkcji, co wiąże się z dodatkowymi wydatkami. Warto również pamiętać o kosztach związanych z przestrzeganiem norm środowiskowych oraz regulacji prawnych dotyczących emisji zanieczyszczeń czy zarządzania odpadami chemicznymi.
Jakie są przyszłe kierunki rozwoju technologii destylacyjnej
Przyszłość technologii destylacyjnej zapowiada się obiecująco dzięki ciągłemu rozwojowi innowacyjnych rozwiązań oraz rosnącemu zainteresowaniu efektywnością energetyczną i ochroną środowiska. Jednym z głównych kierunków rozwoju jest zwiększenie automatyzacji procesów destylacyjnych poprzez zastosowanie sztucznej inteligencji i zaawansowanej analizy danych. Dzięki tym technologiom możliwe będzie lepsze monitorowanie parametrów pracy urządzeń oraz optymalizacja procesów w czasie rzeczywistym, co przyczyni się do zwiększenia wydajności i redukcji kosztów operacyjnych. Kolejnym istotnym trendem jest rozwój materiałów o wysokiej wydajności termicznej i chemicznej, które mogą poprawić efektywność wymiany masy i ciepła w kolumnach destylacyjnych. Technologie takie jak nanotechnologia czy materiały kompozytowe mają potencjał do rewolucjonizacji konstrukcji urządzeń destylacyjnych. Również coraz większa uwaga poświęcana jest aspektom ekologicznym – rozwijane są technologie minimalizujące zużycie energii oraz odpady powstające podczas procesu destylacji.
Jakie są kluczowe aspekty bezpieczeństwa w pracy z destylatorami
Bezpieczeństwo w pracy z destylatorami przemysłowymi jest niezwykle istotnym zagadnieniem, które wymaga szczególnej uwagi ze strony pracodawców oraz pracowników. W procesie destylacji wykorzystywane są substancje chemiczne, które mogą być niebezpieczne dla zdrowia i życia ludzi, dlatego konieczne jest przestrzeganie odpowiednich norm i procedur bezpieczeństwa. Przede wszystkim należy zapewnić odpowiednie szkolenie dla personelu obsługującego urządzenia, aby byli świadomi potencjalnych zagrożeń oraz umieli reagować w sytuacjach awaryjnych. Ważne jest również stosowanie odpowiednich środków ochrony osobistej, takich jak rękawice, gogle czy maski ochronne, które mogą zminimalizować ryzyko kontaktu z niebezpiecznymi substancjami. Kolejnym kluczowym aspektem jest regularna konserwacja i inspekcja urządzeń, co pozwala na wczesne wykrywanie usterek oraz zapobieganie awariom. Należy także zadbać o odpowiednią wentylację w pomieszczeniach, gdzie znajdują się destylatory, aby uniknąć gromadzenia się szkodliwych oparów.